ROMA Werkleiter Bernd Karle und sein Stellvertreter Stefan Naumann im Interview
Individueller Entwurf ermöglicht optimalen Produktionsfluss
Der Hersteller für Sonnenschutzsysteme ROMA hat seinen Standort im sächsischen Oschatz um das Werk 2 erweitert. Entstanden ist eine 10.000 m2 große Produktionshalle mit Verwaltung, die heute den Produktionsfluss optimal abbildet. Das maßgeschneiderte Entwurfskonzept wurde von FREYLER Industriebau Riesa gemeinsam mit ROMA entwickelt und umgesetzt. Wir sprachen mit Werksleiter Bernd Karle und seinem Stellvertreter Stefan Naumann darüber, wie sie die Planungs- und Bauphase erlebt haben.
Redaktion: ROMA ist eine führende deutsche Marke für Sonnenschutzsysteme mit sechs Standorten. Welche Rolle spielt der Standort Oschatz für das Unternehmen?
Bernd Karle: In Oschatz produzieren wir vor allem Halbzeuge für die ROMA Werke in Rostock und Burgau. Ohne unsere Fertigung wären diese Standorte nicht produktionsfähig. Hinzu kommen Rollläden, die wir direkt verkaufen. Das Werk in Oschatz existiert seit Juni 1996 und hat mit der Herstellung von Kunststoffprofilen für Rollläden und Stabware gestartet. Später kamen komplette Kunststoffaufsatzsysteme als Halbzeuge hinzu. In diesem Zuge gab es 2001 eine erste Erweiterung von 3.000 m2, das Werk 1.
Redaktion: Anfang 2024 hat ROMA eine neue, 10.000 m2 große Produktionshalle in Oschatz eröffnet. Was waren die Hauptgründe für diesen Schritt?
Stefan Naumann: Der Neubau dient in erster Linie der Fertigungsoptimierung. Der Standort ist seit 1996 sehr stark gewachsen. Wir haben mittlerweile über 100 Mitarbeiter und es kamen immer neue Maschinen hinzu, für die ein Platz gefunden werden musste. In Folge ließ sich der Fertigungsfluss nicht mehr optimal abbilden. Hinzu kam, dass wir ein etwa 100 Jahre altes Gebäude genutzt haben, das energetisch nicht auf dem Stand der Technik war. Mit einem Neubau konnten wir uns auch energetisch zukunftsfähig aufstellen. Die alte Halle nutzen wir heute nur noch als Kaltlagerhalle.
Redaktion: Wie sind Sie an die Planung des Neubaus herangegangen, und warum fiel die Wahl auf FREYLER als Planungs- und Baupartner?
Stefan Naumann: Auf unserem Grundstück gab es eine große Freifläche zwischen den beiden Hallen, die wir nutzen konnten. Mit Hilfe von Lean Management haben wir zunächst unsere Fertigungsprozesse analysiert und optimiert. Um vom kompletten Erfahrungswissen zu profitieren, haben wir alle unsere Führungskräfte eingebunden. Etwa drei Monate hat diese erste Planungsphase gedauert, in der wir das optimale Funktionslayout aufs Papier gebracht haben. FREYLER hat diesen zweidimensionalen Plan dann baulich in ein dreidimensionales Gebäude umsetzt.
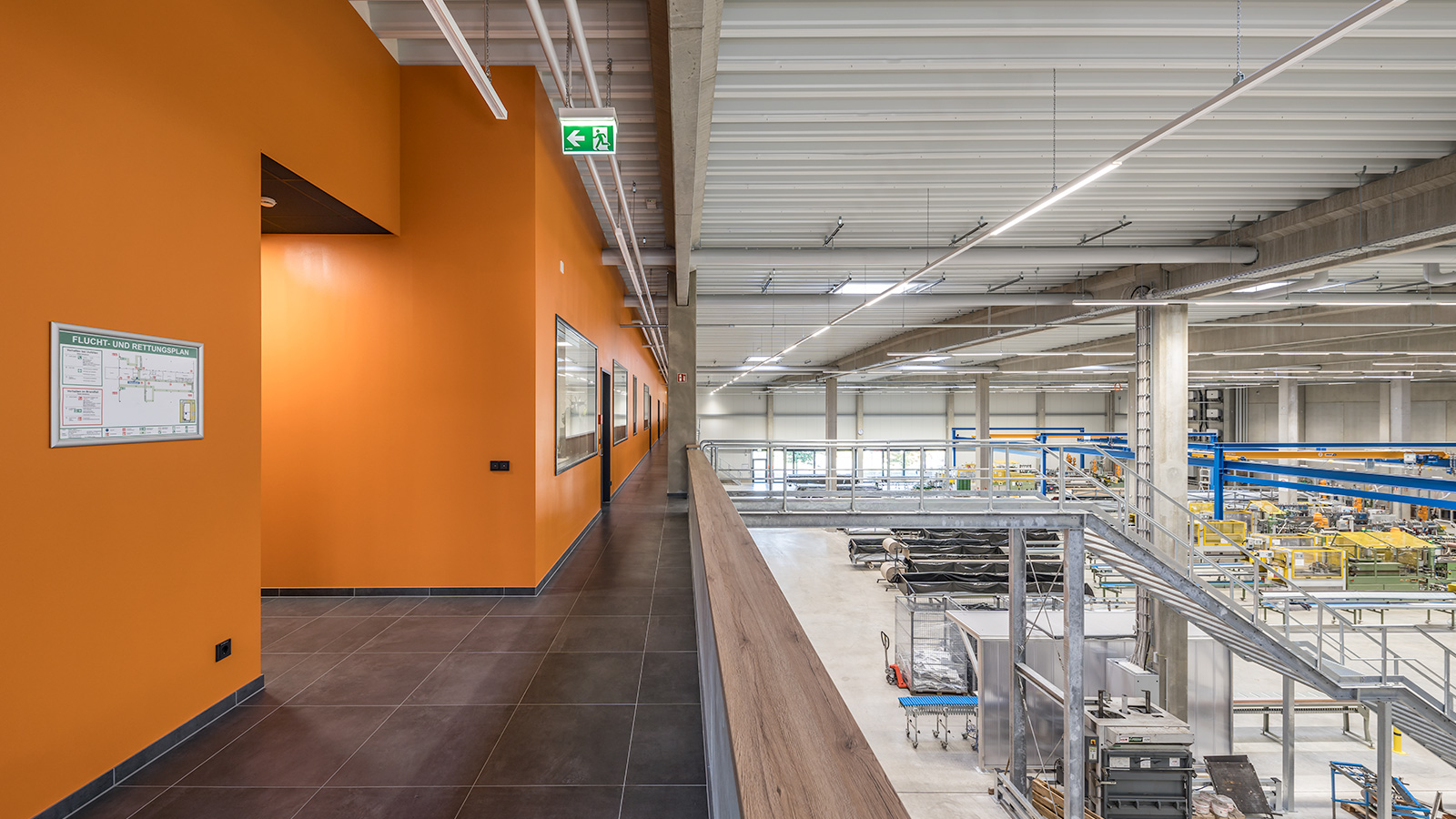
Bernd Karle: Wir hatten mehrere Firmen angefragt, aber FREYLER überzeugte uns durch sein Engagement und die Erfahrung im Industriebau. Nicht zuletzt stimmte auch die Chemie. FREYLER hat nicht versucht, uns ein Konzept von der Stange zu verkaufen, sondern ist auf unsere individuellen Bedürfnisse und Wünsche eingegangen und hat diese in einen passenden Gebäudeentwurf übertragen. Man hat von Anfang an gemerkt, dass es FREYLER wichtig war, das Gebäude so zu planen, dass es für uns perfekt funktioniert.
Redaktion: Wie haben Sie den gemeinsamen Entwurfs- und Planungsprozess mit FREYLER erlebt?
Bernd Karle: Sehr positiv. Das Team von FREYLER, insbesondere unsere Projektleiterin Frau Bär, hat aufmerksam zugehört und unsere Wünsche und Anforderungen in ein individuelles Baukonzept überführt. Die Zusammenarbeit war bereits in der Planungsphase sehr angenehm und kooperativ. Es wurde nach Lösungen geschaut und auch komplexe Themen wie der Brandschutz wurden gemeinsam gelöst.
Redaktion: Gab es im Zuge des Neubaus auch Veränderungen im Bestand?
Stefan Naumann: Ja, die gab es, denn im Zuge des Neubaus haben wir die Fertigung der Systeme räumlich getrennt: Im Werk 1 produzieren wir heute alles auf Losgröße 1, das heißt, dort entstehen Führungsschienen, Revisionsdeckel und Kunststoffrollläden exakt so, wie sie der Kunde auf der Baustelle benötigt. Im neuen Werk 2 fertigen wir alles auf 6 Meter, hier entstehen die Halbzeuge für Burgau und Rostock. Zudem wurde die Folierung in den Neubau verlagert. Im Werk 1 haben wir folglich auch die Prozessabläufen optimiert und die Maschinen neu angeordnet.
Redaktion: Welche Vorteile bietet der Neubau für die Produktion und die Mitarbeiter?
Stefan Naumann: Der Materialfluss verläuft jetzt geradlinig, was die Prozesse erheblich vereinfacht. Und auch die Transportwege wurden optimiert. Früher mussten wir zwischen den beiden Gebäuden Wege von 300 Meter überbrücken, bei Wind und Wetter. In der neuen Halle können wir den Mitarbeitern darüber hinaus einen ganz anderen Komfort bieten, wir arbeiten bei konstanten Temperaturen übers gesamte Jahr hinweg.
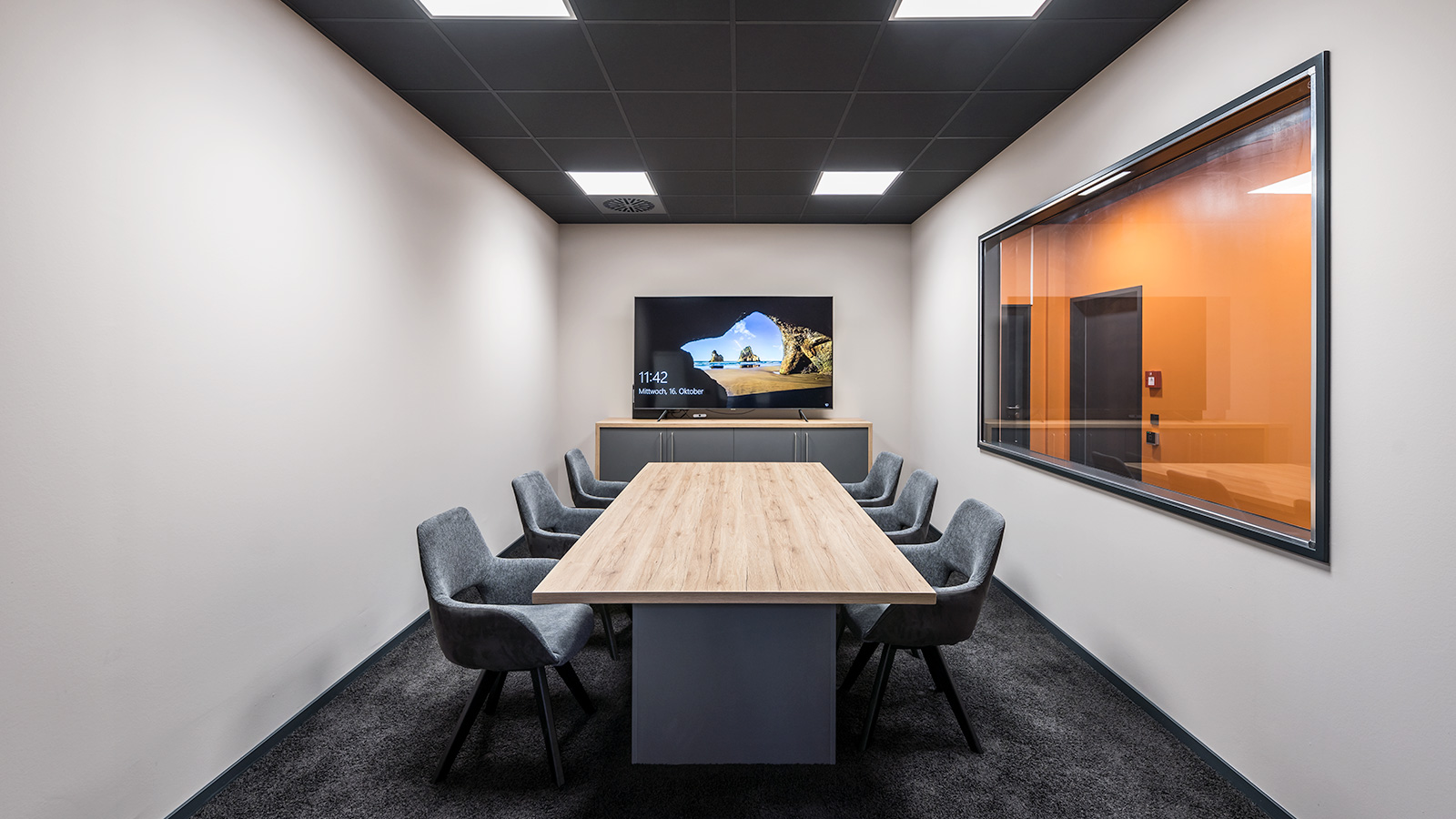
Bernd Karle: Ein weiterer Vorteil ist die Automatisierung: Die Extrusionsanlagen werden jetzt automatisch mit Rohmaterial über drei große Alusilos versorgt. Das ist nicht nur schneller, sondern auch komfortabler, leiser und sauberer.
Redaktion: Ein besonderer Fokus lag auf dem nachhaltigen Energiekonzept für den Neubau. Wie wurden diese Aspekte umgesetzt?
Bernd Karle: Wärmerückgewinnung aus dem Kühlwasser der Produktion nutzen wir bereits seit 1996 und es funktioniert ausgezeichnet. Daher setzen wir auch bei unserem Werk 2 auf Wärmerückgewinnung aus der Extrusion. So können wir heizen und kühlen ohne zusätzliche Energie, die Kälteanlagen zum Kühlen unserer Maschinen werden auch für die Klimatisierung genutzt. Ein Sonnenschutz – natürlich aus dem Hause ROMA – verhindert im Sommer ein unnötiges Aufheizen des Gebäudes.
Stefan Naumann: Zusätzlich deckt eine Photovoltaikanlage mit einer Leistung von 2 Megawatt zukünftig einen Großteil unseres Eigenverbrauchs. Überschüssiger Strom wird ebenfalls zum Kühlen und Heizen genutzt.
Redaktion: Wie verlief die Zusammenarbeit mit FREYLER während der Bauphase?
Bernd Karle: Trotz unerwarteter Herausforderungen wie der schwierigen Baugrundsituation im ehemaligen Militärgebiet verlief der Bauprozess dank der Professionalität von FREYLER reibungslos. Die Zusammenarbeit war sehr gut, das FREYLER Team war immer vor Ort. Einmal in der Woche gab es ein gemeinsames Update – so waren wir immer auf dem aktuellen Stand.
Stefan Naumann: Da wir im laufenden Betrieb gebaut haben, war eine enge Abstimmung wichtig – aufgrund der sorgfältigen Planung und Organisation konnte unsere Produktion problemlos weiterlaufen. Bis heute schätzen wir das gute Miteinander und die lösungsorientierte Zusammenarbeit.
Redaktion: Abschließend: Welche persönlichen Wünsche und Ziele haben Sie für die Zukunft des Standorts in Oschatz?
Bernd Karle: Unser Ziel ist eine gute Auslastung und weiteres Wachstum. Wir haben die Halle für die Zukunft gebaut und sind perfekt aufgestellt, wenn die Baukonjunktur wieder anzieht.
Redaktion: Herzlichen Dank, Herr Karle und Herr Naumann, für das informative Gespräch. Wir wünschen Ihnen weiterhin viel Erfolg und uns allen, dass der Bau wieder an Fahrt gewinnt!